CASE STUDY: Bottom Line Impact
FACILITY: Folding Carton Plant LOCATION: Southeast United States
CHALLENGE
A plant moving an average of 2,100 tons per month was shipping 250-300 tons of loose mixed material locally to be baled versus segregating the material and baling it in-house.
Wilmington Paper, during The Program™ waste audit, determined that revenue was being left on the table.
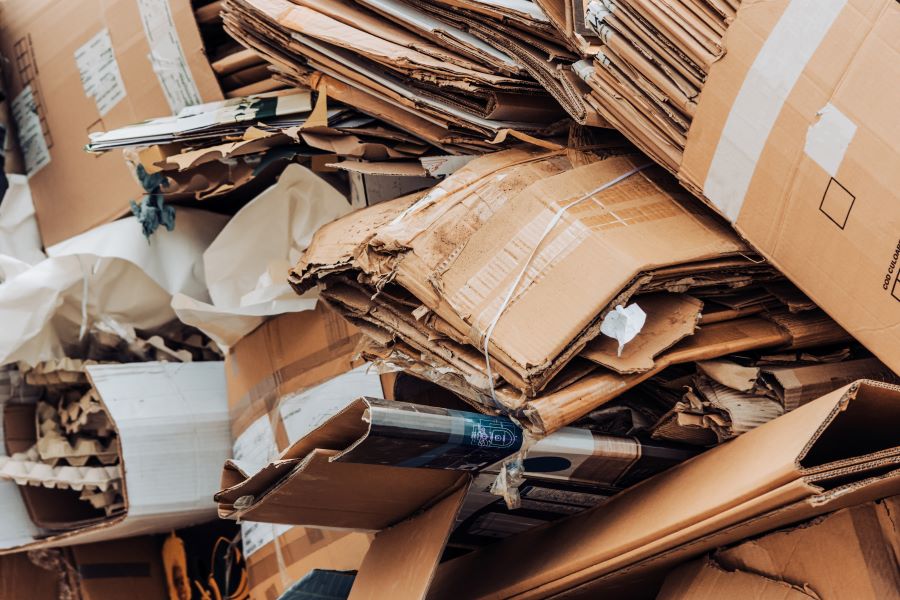
WILMINGTON PAPER RECOMMENDATIONS
Working with the plant management team, Wilmington Paper personnel instituted procedures to ensure that each area of the facility segregates scrap material properly.
Additionally, procedures were put in place to bale the material in-house, ensuring that the plant segregates all SUS, BBC, Unprinted, LP, HP, and Poly SBS at each generation point, so the material was prepped for mill-direct shipments.
THE PROGRAM™ RESULTS
The facility followed the outlined procedures and segregated the material at each generation point, which increased revenue through a higher percentage of mill direct shipments.
Creating a process that enables the material to be baled securely in-house eliminates the need for an additional party.
Plant personnel being placed directly into the baling process enables them to confidently assess the quality of their material bales.